Becoming a Medical Device Reprocessor for the day
Summary:
SickKids staff from a variety of departments were invited to gown up and experience first-hand the valuable role medical device reprocessors (MDR) play at SickKids.
By Amy Naylor, Corporate Communications, Intern
In honour of both Infection Prevention and Control Week and Medical Device Reprocessing Week, SickKids staff from a variety of departments were invited to gown up and experience first-hand the valuable role medical device reprocessors (MDR) play at SickKids.
The MDR team is responsible for the decontamination, preparation, assembly, disinfection, sterilization, storage and distribution of patient care devices. These services are critical to infection prevention and control, and hospital efficiency, but most importantly, these services help contribute to patient safety.
Participants who signed up to experience a new role for the day expected to walk away with some basic knowledge of the technical aspects of the job, some new acquaintances, and a better understanding of how a behind-the-scenes department runs. What came as a surprise was the renewed inspiration for patient care every participant felt as they took off their gowns and headed back to their respective departments.
“I was struck by the level of engagement from the MDR staff, the attention to detail, the safety behaviours – all of those things were really heart-warming from an executive perspective because we recognize that the work that happens here ultimately impacts the patients,” explained Karen Kinnear, Vice-President, Clinical Operations. “This team cares so much, which is so great for patient care.”
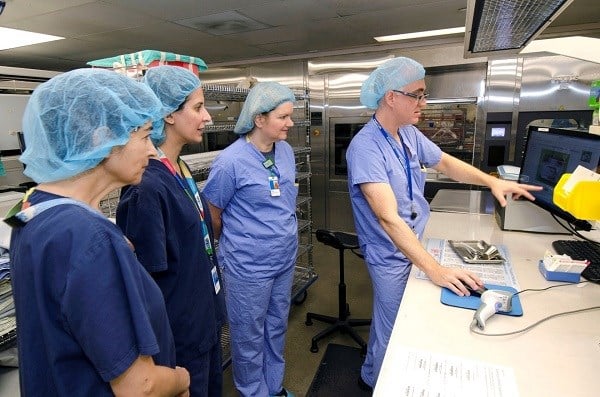
The 50-staff team processes approximately 1,000 medical/surgical sets and products each day. This amounts to 260,000 sets annually, which include about four million individual instruments that must be cleaned, inspected, and sterilized. Each processed product has an individual barcode created which is tracked through each reprocessing step and also allows for quick, real time locating and recalling if necessary. The tracking system eliminates errors which reduces risk.
“Everyone working down here is extremely knowledgeable,” said Elizabeth Pawlica, RN Neurosurgery. “They have a specific way of putting all the medical tools and devices into each procedure tray. For example, you don’t want to clamp the scissors before placing them in the procedure tray, because it’s easier for the surgeons to have them unclamped. The procedure trays are also wrapped in a specific way- the MDR team ensures the procedure trays are wrapped in a manner that allows health care professionals to open them in a sterile manner. So much knowledge and care that we don’t see.”
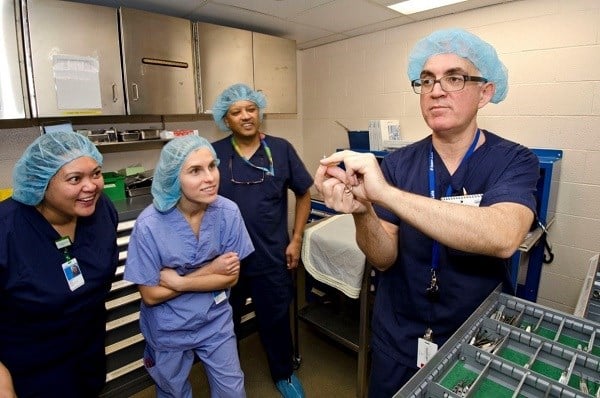
While all of the participants were impressed by the attention to detail and knowledge shown by each member of the MDR team, what was most striking was the thoughtfulness behind every decision they make. Every aspect of the job involves considering how they can make the lives of the clinical care staff easier, resulting in safe, efficient patient care.
“There are certain expectations from clinical end users,” explained Louis Konstant, Clinical Manager, Central Services. “They expect a fold in wrapped packaging will always be in the same place, facing the same way each time they open an instrument set. Even the instruments are all placed in the same position. By taking our time and standardizing our processes, we limit any surprises.”
“I now have a greater appreciation for the work that happens behind the scenes and how this translates to patient safety at the point of care,” remarked Nimira Remtulla, Director, electronic Child Health Network. “I’m blown away at level of attention to detail and the application of Lean principles.”
After a morning of intensive learning and hard work, the participants gathered in a meeting room to eat a well-earned lunch and share what they thought of the experience. When asked what they felt was the biggest learning of the day, Wayne Lee, Director, Diagnostic Imaging, eyed the pizzas and answered:
“I think it’s like ordering a pizza. When I call and place my order, I’ve never thought about how much supply chain is involved in ordering the cheese, the sauce, the dough. I never realized how much work goes into getting it to my door so efficiently. The OR is the same way. I learned a lot today about how much hard, unseen work this team does every day, and how large an impact it has on every level of care.”